モノづくりをしている工場、物流倉庫などでお仕事をされている方へ
仕事の現場の整理整頓は行き届いていらっしゃいますでしょうか?
毎日同じ環境で仕事をしていると、、
非効率な面も日常の仕事の中に溶け込んでしまい、問題点に気付けなくなってしまう場合もあると思います。
特に、機械を扱う製造工場の現場は、整理整頓をしないと、
・ゴミが落ちていても拾わなかったり
・不要なものがどんどん溜まってしまう
・ミスが発生する
・人と機械のパフォーマンスが落ちる
などの悪影響が発生する可能性もあります。
また、機械で製品を作る工場の場合は、怪我や取り返しのつかない事故に発展する可能性もあるので、毎日の取り組みが非常に大切になってきます。
現場作業における整理整頓の主な目的は、「安全管理」と「作業効率アップ」です。1日1%でも効率が上がれば、約5分の時間が作ることができます。1ヶ月にすると(実働20日計算で)100分の時間を作ることができます。
整理整頓をすることでの効率アップはすぐ取り組めるので、設備投資と比べてコストもかからないのでメリット尽くめです^^)
工場での整理整頓が上達する方法を、世界一わかりやすく解説していきます。
理想とする現場環境をつくっていきましょう。
目次 非表示にする
1.現場・物流倉庫の整理整頓の目的について
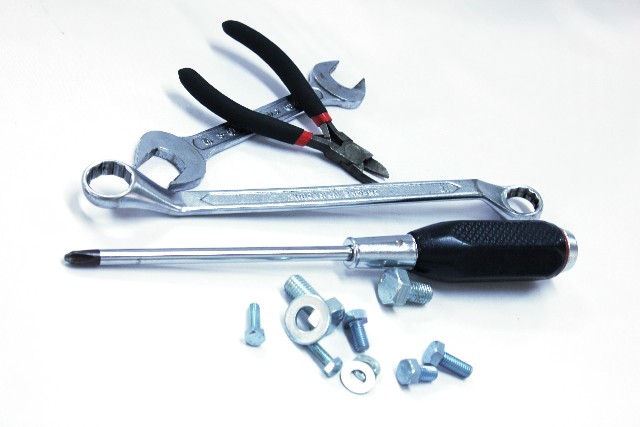
ほとんどの大手企業が取り入れている整理整頓。なぜ、現場や倉庫作業で整理整頓が必要なのでしょうか?
基本をおさえるため、整理整頓の目的を確認していきましょう。
機械を使う製造現場の場合、怪我や人身事故は絶対に防がなくてはなりません。
まず、重大な事故が発生した場合そのまま何もなかったように製造を続けられません。
必ず改善をして、同じ事が起こらないように対策をする必要があります。
ケガをした本人はもちろん、改善するまで作業がストップするなどの影響がでる可能性もあります。
一事が万事、小さな問題が大変な事態を招くこともあります。人身事故を防ぐことは、製造現場の最優先事項ですよね!
その為にも、不要なモノを捨て、必要なモノは置き場所を決めて保管することが非常に大切です。整理整頓の基本ですね^^
もう一つの目的は、整理整頓を通して徹底してムダを排除し、作業効率・生産効率を上げる事です。
例としては、
「ものを探すムダをなくす」
「商品のロスのムダをなくす」
「作業スペースを確保して生産効率を上げる」
「正確性を上げる」
などの項目が挙げられます。
徹底してムダをなくすことで、必然的に、且つ単純に生産スピードがあがます。
結果的にゆとりも生まれて未来づくりに投資する時間を作ることができます。
効率アップだけでなく、安全面の向上にも大いに関係しますので、整理整頓は人を守るためにも大変重要な要素となります。
2.現場で役に立つ整理整頓の5つのコツ!
現場作業で今日から使える整理整頓のコツがあります。
安全管理や効率アップのために、取り入れできるものがあったらチェックして実践していきましょう。
5つ項目がありますので、取り入れできるものはすぐ実践してみてはいかがでしょうか?
整理整頓をいきなり始めるのではなく、必ず計画を立てましょう。
はじめに整理整頓を「いつ、どの場所を、だれが、どんなものを、どうするのか」の計画を立ててます。できれば、次回以降の予定も決めましょう。
実施する時には、どんな点に注意するのかを事前に話し合っておきましょう。
また、実施後にはかならず反省会を行い、かかった時間や、気がついた事などをお互いにフォードバックします。次回以降の整理整頓につなげる為ですね。
キレイな状態を維持する仕組みをみんなで考えていきましょう。
製造現場でよく取り入れている「5S活動」はご存知ですか?
ご存知の方もいらっしゃる通り、職場環境を維持・向上するためのスローガンで「整理」「整頓」「清掃」「清潔」「しつけ」、これら5つのことです。簡単に説明させていただきますね。
「整理」→必要なものと不要なものをわけて、不要なものを処分する事。
「整頓」→必要なものを取り出しやすい位置に置く。また、誰でも取り出しやすいように明記すること。
「清掃」→掃除をして、キレイな状態を保つこと。
「清潔」→上の3つ(整理・整頓・清掃)を継続すること。計画を立てて実行すること。
「しつけ」→決められたことを、いつも正しく守る習慣をつけること。
基本的なことですが、5Sができると現場環境がガラッと変わります。人によっては、さらに良い環境にする為に前向きな意見がいただけるかもしれませんね。
整理整頓を実施するスタッフ全員で言葉の定義を必ず確認しましょう。
トヨタ式の5Sに関する記事はこちらから!!
→トヨタ流5Sの取り組み【仕事の効率がドカンと上がる整理整頓】
整理整頓をはじめる時に絶対やってはいけないこと、それは不要なものも一緒に整頓してしまうことです。したがって、5Sを実施する時には必ず「整理」からはじめましょう。
不要なものをチェックする時の方法はいくつかあります。私も経験があるオススメの方法をご紹介させていただきます。
それは「不要テープ」作戦です。赤いテープ(シールでもいいのですけど)を用意して、工場内の「不要」「どうするか迷う」もの全てに貼っていきます。5〜6人で行うと、複数の価値観で判断ができます。また、他の人の作業空間と相対的に見比べることができるのでオススメです。定例で行えるように計画を立て、リーダー以外は毎回違うメンバーで実施するのも有効だと思います。
テープ(シール)を貼り終えたら、同じルートで2週目を回ります。ここで整理整頓を実施します。
はじめに「不要」なものは、その場所から物理的に取り除きます。これだけでスペースが生まれます。
「迷うもの」は保留期間を決めます。すぐ使わないもの、いつか使うもの、など毎日使わないものが対象になる場合が多いと思います。モノを「いつ使うか」を明確にすると、不思議と置き場所が決まってきます。
自分の動作範囲、つまりすぐ手の届く位置に一番使う物を置き、すぐ使わないものは多少距離があっても別に置き場所を作って保管をするのも、方法のひとつだと思います。作業をする人が最も効率の良く製品が作れる位置を選択しましょう。
次に整頓ですが、モノ一つ一つの置き場所を決めてあげます。
ジャンルで分ける、
使用頻度でわける、
大きさでわける、
切り口はいろいろあると思いますが、最も効率の良い方法にしましょう。私のルールは、「モノを使う場所の近く」に保管するです。移動するだけで時間ロスだからです。
同時に、自分以外の人でも整頓ができるように、見える化をしていきましょう。言葉の通り、整頓ルールを文字などで目に見えるようにすることです。保管マップを作ると、あなたが居ない時でも整頓ができます。
保管マップは、あなたの身の回りの地図のようなものです。どの場所に何があるか事前にわかると、探し物の時に時間ロスがすくなくてすみます。
私が今まで関わってきた製造現場では、5S活動を毎日10分程度行っていました。5Sをしなかった時、後から時間をロスする可能性について共通認識ができているからです。5Sで言うと「しつけ」にあたります。
全員での意識確認とともに自ら率先して実行できるように、ハウツー本で取り入れられそうなものがあったら試しながら実行していきましょう。そして、効果のあったもの、全体で取り入れた方が効果が高まる方法があれば同僚にも勧めてあげましょう。
3.まとめ
いかがでしたでしょうか?
現場作業では「安全管理」と「作業効率アップ」を追求し続けるだけで、職場・現場環境は全く変わってきます。
もちろん、製造現場だけでなく、物流倉庫、工事現場、オフィス、自宅でも取り入れられるノウハウです。
また、一時的なことではなく、全員で継続して取り組むことが大切です。全員でやると決めたのに整理整頓が苦手な人や、サボってやらない人がいたら必ず声をかけて一緒に実行しましょう。大事なのは注意することではなく、全員で実施する事。
コミュニケーションを通じて、チームワークも一緒に高めていきましょう!
整理整頓を通して、有意義な時間を過ごせますように^^
こちらの記事もおすすめです!
最後までお読みいただきありがとうございます!
ブログランキングに参加していますので、もし少しでもお役に立てましたら
下のバナーを応援クリックいただけると更新の励みになります(*^^*)
ありがとうございました。
参考に、させていただきます。
謙二さま
コメントをいただき嬉しい限りです!
作業効率は、ほんの少しの改善でも、
長い目でみると大きな差になりますよね^^
ご参考になれば幸いです!